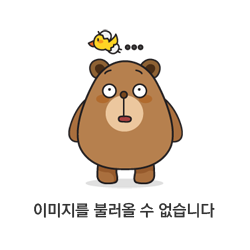
(Economist, Sep/16/2024) The semiconductor industry faces its biggest technical challenge yet
네덜란드 에인트호번에 위치한, 넓고 청결한 건물 내부에서 ASML이 설계한 최신 거대한 장비가 조용히 작동 중이다. 이 장비는 무게가 150톤에 달하며, 크기는 2층 버스만 하다. 이 도구는 인간이 빙하기부터 해오던 일을 현대적으로 수행하는 최신 방법을 제공한다. '돌에 글을 새기는 일', 즉 리소그래피(lithography)를 말한다. 여기서 돌은 실리콘이고, 글을 새기는 도구는 빛이다.
이 기계는 매초 50,000개의 주석 방울을 진공 챔버에 발사한다. 레이저가 각 방울을 섭씨 220,000도까지 가열하는데, 이는 태양 표면 온도의 40배에 해당한다. 이 과정에서 주석 방울은 플라즈마로 변하며, 극도로 짧은 파장의 빛(극자외선, EUV)을 방출한다. 이 좁은 빔의 빛은 일련의 거울에 의해 반사되는데, 이 거울들은 표면이 수십 피코미터(1조분의 1미터)까지 매끄럽다. 그런 뒤, 이 빛은 칩 회로의 청사진이 담긴 마스크에 맞춰진다.
EUV 광선은 마스크에서 반사되어 **포토레지스트**라고 불리는 감광성 물질로 코팅된 실리콘 웨이퍼에 회로 설계를 투사한다. 웨이퍼는 패턴을 여러 번 정확하게 인쇄할 수 있도록 매우 정밀하게 이동되며, 한 장의 웨이퍼는 수백 개의 칩을 제작하는 데 사용될 수 있다. 일반적으로 빛에 노출된 포토레지스트는 씻겨 나가면서 실리콘 웨이퍼 위에 ‘스텐실’이 형성된다. 이후의 장비들이 이 스텐실을 따라 재료를 깎아내거나 이온을 주입하거나 금속을 증착하여 칩의 한 층을 만들어낸다. 그런 다음 새로운 포토레지스트 층이 추가되고, 새로운 패턴이 투사되며, 또 한 번 에칭이 이루어진다. 현대 칩은 이러한 인쇄 과정이 수십 겹으로 반복되기도 한다.
ASML의 최신 EUV 리소그래피 기계는 대당 3억 5천만 달러 이상을 넘는다. 이는 반도체 산업의 역동성을 잘 보여준다. 칩의 주요 전자 부품인 트랜지스터가 작아질수록, 이를 제작하는 도구와 공장은 더 커지고 비싸지고 있다. 미국 싱크탱크인 프로그레스 연구소의 브라이언 포터는 1960년대 후반에 반도체 제조 공장(팹)을 건설하고 장비를 갖추는 데 오늘날의 가치로 약 3,100만 달러가 들었다고 추정한다. 반면, 대만의 거대 기업 TSMC가 애리조나에 새로 짓고 있는 최신 팹은 각각 200억 달러에 달할 예정이다.
Itsy bitsy teeny weeny
이제 이 팹에서 수조 개씩 만들어지는 트랜지스터는 스위치 역할을 한다. 각각의 트랜지스터에는 **소스**(source)와 **드레인**(drain)이라 불리는 두 단자가 있으며, 이 단자들은 실리콘 채널로 분리되어 있다. 이 채널 위에는 **게이트**(gate)라는 세 번째 단자가 위치하여 소스와 드레인 사이의 전류 흐름을 조절한다. 게이트에 전압이 가해지면 소스에서 드레인으로 전류가 흐르고, 전압이 없으면 전류가 멈춘다. 이 켜짐과 꺼짐 상태는 2진법의 1과 0에 해당한다.
컴퓨터 프로그램이 아무리 마법처럼 보일지라도, 그 프로그램이 실행되는 하드웨어는 근본적으로 회로에 따라 연결된 스위치들이 켜지고 꺼지는 과정에 불과하다. 논리 게이트라고 불리는 간단한 회로는 트랜지스터를 결합해 이진 논리의 기본 기능을 제공한다. AND 게이트는 두 입력이 모두 1일 때 출력이 1이 되고, OR 게이트는 어느 하나의 입력이 1일 때 출력이 1이 된다. NOT 게이트는 1을 0으로, 0을 1로 변환한다. 이러한 논리 게이트들은 더 복잡한 회로로 결합될 수 있으며, 이러한 회로들은 다시 강력한 처리 칩으로 통합될 수 있다.
1965년 고든 무어의 원래 관찰은 칩 제조 기술이 발전함에 따라 트랜지스터가 작아졌고, 그 결과 더 많은 트랜지스터를 더 저렴하게 만들 수 있다는 것이었다. 1974년, IBM의 엔지니어 로버트 데나드는 더 작은 트랜지스터가 단순히 단위 비용을 줄이는 것만이 아니라 성능도 향상시킨다는 점을 발견했다. 소스와 드레인 사이의 거리가 줄어들수록 스위치의 속도가 증가하고, 에너지 소비는 감소한다. 이 관찰은 "데나드 스케일링"으로 알려져 있으며, 무어의 법칙이 가져오는 이점을 더욱 증폭시킨다.
1970년에 게이트 길이(소스와 드레인 사이의 거리)는 10마이크론(10만분의 1미터, 또는 10,000nm)이었다. 그러나 2000년대 초반에는 이 길이가 90nm까지 줄어들었다. 이 수준에서는 양자 효과로 인해 트랜지스터가 꺼져 있을 때도 두 단자 사이에 전류가 흐르게 된다. 이러한 누설 전류는 사용되는 전력을 증가시키고 칩이 과열되는 문제를 야기한다.
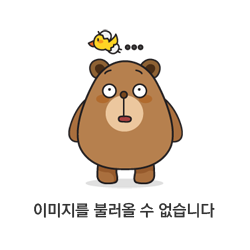
반도체 제조업체들에게 이것은 그들이 오랫동안 누려왔던 "거의 공짜"와 같던 혜택이 끝나가고 있다는 초기 신호였다. 트랜지스터는 여전히 더 작게 만들 수 있었지만, 누설 전류로 인해 칩의 전압을 더 이상 낮출 수 없게 되었다. 이는 결과적으로 칩의 전력 소모를 이전처럼 줄일 수 없다는 것을 의미했다. 이 "전력 장벽"은 데나드 스케일링의 끝을 알렸으며, 트랜지스터 크기는 계속 작아졌지만 칩 속도는 더 이상 빨라지지 않았고 전력 소모가 큰 문제가 되었다.
성능을 계속해서 개선하기 위해 설계자들은 칩의 논리 게이트와 기타 요소들을 다중 연결된 처리 장치, 즉 **"코어"**에 배치하기 시작했다. 여러 개의 코어를 사용하면 프로세서는 여러 애플리케이션을 동시에 실행하거나, 하나의 애플리케이션을 병렬 처리 방식으로 나누어 더 빠르게 실행할 수 있다.
이 접근 방식 덕분에 스위치의 작동 속도가 더 이상 증가하지 않더라도 성능을 계속해서 향상시킬 수 있었다. 그러나 트랜지스터가 사용하는 전력이 더 이상 감소하지 않는 문제는 해결되지 않았다. 트랜지스터 수가 계속 증가함에 따라 칩 설계자들은 과도한 열로 인해 칩이 녹는 것을 방지하기 위해 "다크 실리콘"이라 불리는 칩의 일부를 꺼놓는 방법을 사용했다. 이로써 불필요한 발열을 줄이면서도 성능 향상을 유지하려는 노력이 이어졌다.
누설 전류 문제를 해결하기 위해, 전통적인 트랜지스터 구조를 포기해야 했다. 기존 구조에서는 전도 채널이 칩 표면에 평행하게 위치하고, 제어 게이트는 그 위에 놓여 있었다. 2011년 인텔은 채널이 물 위에 떠 있는 지느러미처럼 위로 솟아올라 게이트를 통과하는 새로운 디자인을 도입했다(그림 참조). 이 방식은 게이트가 꺼져 있을 때도 채널에 더 강한 제어력을 발휘할 수 있게 했다. 이러한 "핀펫"(finfets) 구조는 트랜지스터를 더 작게 만드는 것을 가능하게 했다. 새로운 트랜지스터는 이전 세대보다 누설 전류가 적고, 소비 전력은 약 절반으로 줄어들었다. 현재 최첨단 공정에서는 속도를 높이기 위해 트랜지스터당 두세 개의 핀을 사용하는 경우가 많다. 핀펫 덕분에 게이트 길이는 약 16nm까지 줄어들 수 있었지만, 옆에 배치할 수 있는 핀의 수에는 한계가 있다.
게이트 길이를 더 줄이기 위한 다음 단계는 채널을 칩 표면에서 완전히 들어 올려, 게이트가 모든 면에서 채널을 둘러싸도록 만드는 것이다. 이러한 트랜지스터는 "게이트 올 어라운드"(GAA)라고 불리며, 이를 최초로 구현한 것은 한국의 대기업 삼성이다. 삼성은 최신 칩에서 GAA 트랜지스터를 도입했고, 인텔과 TSMC도 곧 뒤따를 것으로 예상된다. 벨기에의 반도체 연구 기관인 imec은 GAA가 업계를 이끌며 이 10년의 끝까지 갈 것이라고 전망하며, 그 시점이 되면 게이트 길이가 현존하는 기술로 에칭할 수 있는 최소 크기에 가까워질 것이라고 예측한다.
이 지점 이후에는 트랜지스터 밀도를 높이기 위한 유일한 방법이 칩을 재설계하여, 기존에 나란히 배치되던 일부 트랜지스터를 위아래로 쌓는 것이다. 3차원 구조로 전환하면 칩 제조업체들은 수평 방식보다 더 많은 게이트를 집적할 수 있다. 예를 들어, 인텔은 트랜지스터를 쌓음으로써 가장 간단한 논리 게이트인 인버터를 일반적으로 필요한 공간의 절반만으로도 제작할 수 있다고 설명한다.
트랜지스터를 쌓아 올리더라도 더 작은 공간에 집적하려는 필요성은 계속된다. 트랜지스터의 게이트 길이가 10nm에 가까워지면, 전류가 게이트를 통과하는 실리콘 채널의 두께는 4nm 이하로 줄어들어야 하며, 이로 인해 누설 전류 문제가 더욱 심각해진다. 이에 대한 반도체 업계의 해결책은 실리콘을 두께가 거의 없는 재료로 대체하는 것이다. 원자 몇 개의 폭에 불과한 두께, 즉 몇 나노미터 두께의 재료로 만들어진 회로는 트랜지스터가 꺼졌을 때 전류가 새는 문제 없이 더 작게 제작할 수 있도록 해줄 것이다.
Thinning out
얇게 만드는 과정에서 실리콘을 대체할 이차원(2D) 물질 후보 중 하나는 전이 금속 칼코겐화합물(TMDs)이라고 불리는 물질로, 이들은 원자 세 개 두께의 층으로 만들 수 있다. 실리콘을 대체할 수 있는 수백 가지의 TMD 반도체 중에서 가장 유망한 세 가지는 몰리브데넘 이황화물(MoS₂), 텅스텐 이황화물(WS₂), 그리고 텅스텐 셀레늄화물(WSe₂)이다.
실리콘을 대체할 또 다른 유력 후보는 탄소 나노튜브이다.
하지만 이러한 2D 물질들이 실리콘을 대체하기 위해서는 해결해야 할 몇 가지 어려움이 있다. 첫 번째 문제는 이 물질들이 너무 얇아 금속 배선과 연결하는 것이 어렵다는 점이다. 또 다른 문제는 이러한 물질을 사용하여 300mm 웨이퍼(칩 제조의 표준 크기) 전반에 걸쳐 신뢰성 있게 칩을 제작하는 것이다. 또한, 칩 설계는 두 가지 다른 유형의 트랜지스터에 의존하는데, 실리콘에서는 두 유형을 모두 쉽게 만들 수 있는 반면, 새로운 물질들은 주로 한 가지 유형의 트랜지스터에만 더 적합한 경향이 있다.
실리콘을 대체할 또 다른 유력 후보는 탄소 나노튜브(CNT)이다. 탄소 나노튜브는 탄소 원자들이 말려서 형성된 지름 1.5nm 크기의 실린더 형태의 구조다. CNT 트랜지스터는 일반적인 트랜지스터와 비슷하게 소스, 드레인, 게이트 단자가 반도체 재료로 만들어지지만, 채널은 일반 트랜지스터의 실리콘 채널 대신 작은 나노튜브들이 평행하게 배열되어 있다. 나노튜브의 매끄러운 구조 덕분에 전하가 실리콘 채널을 통과할 때보다 3배 빠르게 켜고 끌 수 있다. 또한, 채널이 얇아 게이트가 채널을 더 잘 제어할 수 있어 누설 전류를 줄이고 에너지 효율성을 높일 수 있다.
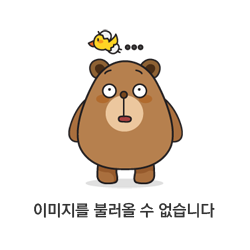
스탠퍼드 대학교의 에릭 팝은 파운드리들이 탄소 나노튜브(CNT)보다 2D 반도체를 선호하는 경향이 있다고 믿고 있다. 그 이유는 2D 반도체가 실리콘과 더 쉽게 제조되고 통합되기 때문이다. CNT는 더 나은 성능을 제공할 수 있고 게이트 올 어라운드(GAA) 트랜지스터에 이상적이지만, 제조 과정에서 제어하기가 어렵다.
나노튜브를 제작하는 일은 간단하지 않다. CNT는 제조 과정에서 발생하는 결함에 민감하며, 이러한 결함은 전기적 특성을 변화시킨다. 대부분의 나노튜브는 게이트 전압에 따라 켜지고 꺼지는 반도체 성질을 가지지만, 약 3분의 1은 금속 구조로서 항상 켜져 있고 게이트로 제어할 수 없다. 또한, 소스와 드레인 사이에 나란한 선으로 정확하게 평행하게 나노튜브를 배열하는 것도 어려운 과제다.
2013년, 현재 MIT에 있는 맥스 슐레이커는 스탠퍼드 대학교의 수바사시시 미트라와 필립 웡과 함께 탄소 나노튜브(CNT) 트랜지스터를 사용해 최초의 마이크로프로세서를 제작했다. 연구진은 일정 수의 CNT가 제대로 작동하지 않더라도 기능할 수 있는 "결함 내성" 프로세서를 설계했다. 2019년까지 슐레이커는 14,000개의 CNT 트랜지스터로 구성된 마이크로프로세서를 개발했다(이는 1978년 인텔에서 출시된 8086 칩의 절반 수준이다). 2023년에는 베이징 대학교 연구진이 CNT를 사용하여 10nm 실리콘 노드 크기로 축소할 수 있는 제조 기술을 통해 트랜지스터를 제작했다. 이러한 결과는 기본적으로 보일 수 있지만, CNT가 실리콘을 대체할 수 있는 잠재력을 강조하는 중요한 진전이다.
1959년, 물리학자 리처드 파인만은 나노기술 시대를 예고하는 강연을 했다. 그는 "원자를 하나씩 우리가 원하는 방식으로 배열할 수 있다면 어떻게 될까?"라는 질문을 던졌다. 오늘날 반도체 소자의 특징이 원자적 크기에 도달한 상황에서, 그 질문에 대한 답은 명확하다: 더 작은 트랜지스터를 만드는 것이다.
'미주연 리포트' 카테고리의 다른 글
[Silicon returns to Silicon Valley] 디지털 컴퓨팅을 넘어선 가능성 (3) | 2024.09.20 |
---|---|
[Silicon returns to Silicon Valley] AI는 칩 아키텍처와 소프트웨어를 밀접하게 결합시키고 있다 (7) | 2024.09.20 |
[Silicon returns to Silicon Valley] 데이터 센터를 과열시키지 않으면서 더 강력한 칩을 만드는 방법 (2) | 2024.09.20 |
[Silicon returns to Silicon Valley] 노드 이름이 실제 트랜지스터 크기를 반영하지 않는다 (2) | 2024.09.20 |
[Silicon returns to Silicon Valley] AI가 반도체를 컴퓨터 기술의 중심으로 (5) | 2024.09.19 |
연초이후 약 3배 상승한 숨은 AI 수혜주 : 탈런 에너지 (2) | 2024.09.19 |
연준의 금리인하 이유와 전망 (8) | 2024.09.19 |
연준 금리 인하의 결과 (7) | 2024.09.17 |